Could US10190201B2 face validity concerns? This patent, titled Copper Alloy for Electronic Applications, is currently the subject of litigation in Materion Corporation v. Lebronze Alloys et al., filed in the U.S. District Court for the District of Delaware. It is one of three patents in dispute, alongside US10858723B2 and US11008818B2.
US10190201B2 claims a specialized copper alloy designed for electronic applications, but a key legal question remains. Does prior art exist that could challenge its validity? If relevant references surface, they could undermine the patent’s novelty, potentially impacting the case’s outcome.
In this article, we utilize the Global Patent Search tool to uncover potential prior art that may be relevant to US10190201B2. Let’s examine the findings.
Understanding Patent US10190201B2
Patent US10190201B2 describes a process for manufacturing spinodal copper-nickel-tin alloys with enhanced impact strength, yield strength, and ductility. The patent outlines a specialized treatment process involving solution annealing, cold working, and spinodal hardening. This results in a material with superior mechanical properties compared to conventional copper-based alloys.
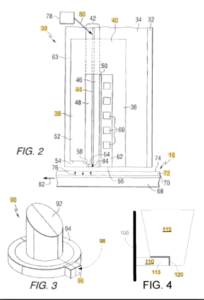
Source – US10190201B2
Its key features include:
#1. Spinodal hardening process – A unique heat treatment method that enhances the alloy’s strength while maintaining ductility.
#2. Optimized composition – The alloy consists of 5-20% nickel, 5-10% tin, and the balance is copper, with minor elements like boron, zirconium, and magnesium improving its properties.
#3. Multi-step manufacturing method – The process includes homogenization, hot working, solution annealing, cold working, and spinodal hardening, each step fine-tuning the material’s microstructure.
#4. High-performance applications – The resulting alloy has high yield strength (≥110 ksi), superior impact toughness (≥12 foot-pounds), and excellent ductility, making it ideal for oil and gas drilling equipment.
By analyzing prior art, we can determine whether US10190201B2 genuinely represents an innovative leap or if pre-existing technologies anticipate its claims.
Potential Prior Art References for US10190201B2
#1. JP2007531824A
This reference discloses a copper-nickel-tin-lead alloy manufactured using continuous casting, static billet casting, or spray forming. However, the presence of lead (Pb) as a component distinguishes it from US10190201B2, which focuses solely on copper-nickel-tin
compositions.
Why this qualifies as Potential Prior Art?
- Overlapping processing steps – The reference discusses casting, homogenization, hot working, cold working, and spinodal hardening, similar to US10190201B2.
- Partial Alloy Composition match – While the reference includes 5-20% nickel and 5-10% tin, it also contains lead (Pb), which is absent in US10190201B2.
- Spinodal Hardening– The reference explicitly describes spinodal decomposition to enhance mechanical properties, aligning with US10190201B2.
- Tensile strength alignment – The reference states an ultimate tensile strength exceeding 120 ksi, matching the claimed property in US10190201B2.
Feature Mapping Results
Feature | Disclosure Status |
The method involves casting a copper-nickel-tin alloy | Partially Disclosed |
The alloy is homogenized | Fully Disclosed |
The homogenized alloy is hot worked to obtain a reduction ratio of minimum 5:1 | Partially Disclosed |
The hot worked alloy is solution annealed at 1470°F to 1650°F | Partially Disclosed |
The solution annealed alloy is cold worked until a reduction of area of 15% to 80% occurs | Partially Disclosed |
The alloy is spinodally hardened after cold working | Fully Disclosed |
The alloy contains 5-20 wt% nickel | Fully Disclosed |
The alloy contains 5-10 wt% tin | Fully Disclosed |
The alloy contains minor additions of boron, zirconium, iron, niobium, manganese, and/or magnesium, each not exceeding 0.3 wt% | Partially Disclosed |
The balance of the alloy composition is copper | Fully Disclosed |
The alloy has a 0.2% offset yield strength of at least 110 ksi | Fully Disclosed |
The alloy has an ultimate tensile strength of at least 120 ksi | Fully Disclosed |
Key Excerpt from the Reference:
“Alloys containing copper, nickel, and tin as main components are widely used. These mechanical properties are further improved by known thermal aging treatments such as spinodal decomposition. For alloys containing 15% nickel by weight and 8% tin, mechanical resistance can reach 1500 MPa (217 ksi).”
#2. JP2011503366A
This reference discloses a high-strength Ni-Fe-Cr-Mo-Cu alloy designed for oil and gas applications. It describes solution annealing, aging, and heat treatment methods to optimize strength and corrosion resistance.
Why this qualifies as Potential Prior Art?
- High-strength alloy for oil & gas use – The reference describes high-strength, corrosion-resistant alloys designed for harsh drilling environments, similar to the applications of US10190201B2.
- Advanced heat treatment process – It discusses solution annealing and aging treatments, which may offer partial similarities to spinodal hardening.
- Comparable mechanical strength – The reference states an ultimate tensile strength exceeding 120 ksi and a yield strength of at least 145 ksi, which surpasses US10190201B2’s requirements.
- Nickel-based alloy with copper additions – While not a Cu-Ni-Sn alloy, the reference does contain nickel and small amounts of copper (up to 3%), which may provide indirect relevance.
Feature Mapping Results
Feature | Disclosure Status |
The hot worked alloy is solution annealed at 1470°F to 1650°F | Partially Disclosed |
The alloy contains minor additions of boron, zirconium, iron, niobium, manganese, and/or magnesium, each not exceeding 0.3 wt% | Partially Disclosed |
“Alloys used in harsh oil and gas environments must withstand corrosive conditions. The goal of this study was a minimum yield strength of 145 ksi. The alloy composition includes Fe 0-15%, Cr 18-24%, Mo 3.0-9.0%, Cu 0.05-3.0%, and balance Ni.”
#3. BRPI0619666A2
This reference discloses a high-efficiency corrosion-resistant alloy composed primarily of nickel, iron, chromium, molybdenum, and copper. The alloy is designed for high thermal stability and corrosion resistance, making it suitable for demanding environments such as oil and gas applications.
Why this qualifies as Potential Prior Art?
- Solution annealing similarities – The reference describes solution annealing followed by water or air cooling, a process that partially overlaps with US10190201B2.
- Ultimate Tensile Strength alignment – The reference states an ultimate tensile strength exceeding 120 ksi, which matches a key feature of US10190201B2.
- High-strength alloy system – The reference achieves mechanical properties comparable to US10190201B2, although its composition differs significantly.
- Incidental copper content – The reference mentions copper as part of the alloy composition, though only in minor amounts and not as the base metal.
Feature Mapping Results
Feature | Disclosure Status |
The hot worked alloy is solution annealed at 1470°F to 1650°F | Partially Disclosed |
The alloy has a 0.2% offset yield strength of at least 110 ksi | Partially Disclosed |
The alloy has an ultimate tensile strength of at least 120 ksi | Fully Disclosed |
#4. CN105714148B
This reference describes a high-strength, spinodal decomposition-reinforced copper-nickel-tin alloy. The alloy is processed through casting, homogenization, hot extrusion, and solution annealing, followed by aging treatments to enhance its mechanical properties.
Why this qualifies as Potential Prior Art?
- Casting and processing steps match – The reference details casting, homogenization, hot extrusion, and solution treatment, similar to US10190201B2.
- Spinodal hardening is described – The reference explicitly mentions spinodal decomposition as a strengthening mechanism, aligning with US10190201B2.
- Nickel and Tin Composition overlaps – The alloy contains 14-16 wt% nickel and 7-9 wt% tin, which falls within the 5-20 wt% Ni and 5-10 wt% Sn range in US10190201B2.
- Hot Working exceeds Minimum Reduction Ratio – The reference describes hot extrusion with a reduction ratio of 17, which surpasses the 5:1 ratio required in US10190201B2.
Feature Mapping Results
Feature | Disclosure Status |
The method involves casting a copper-nickel-tin alloy | Fully Disclosed |
The alloy is homogenized | Fully Disclosed |
The homogenized alloy is hot worked to obtain a reduction ratio of minimum 5:1 | Fully Disclosed |
The hot worked alloy is solution annealed at 1470°F to 1650°F | Fully Disclosed |
The alloy is spinodally hardened after cold working | Fully Disclosed |
The alloy contains 5-20 wt% nickel | Fully Disclosed |
The alloy contains 5-10 wt% tin | Fully Disclosed |
The alloy contains minor additions of boron, zirconium, iron, niobium, manganese, and/or magnesium, each not exceeding 0.3 wt% | Partially Disclosed |
The balance of the alloy composition is copper | Fully Disclosed |
The alloy has an ultimate tensile strength of at least 120 ksi | Partially Disclosed |
Key Excerpt from CN105714148B
“As a kind of amplitude modulation (Spinodal decomposition) reinforced alloy, Cu-Ni-Sn alloy strength and toughness mainly depend on the alloy composition, preparation process, and heat treatment process. Among them, the optimization of composition design is an important way to improve the performance of such alloys. The strength of Cu-Ni-Sn alloy increases with the increase of Ni and Sn content and reaches the peak when Ni content is 15wt% and Sn content is 8wt%.”
#5: JPH0413826A
This reference describes a high-strength copper alloy optimized for machining, specifically a Cu-Mn-Al alloy. It details casting, hot rolling, cold rolling, and annealing, but does not mention a copper-nickel-tin alloy or spinodal hardening.
Why this qualifies as Potential Prior Art?
- Processing Overlaps – The reference describes casting, hot rolling, and cold rolling, similar to US10190201B2.
- Cold Working Matches Reduction Range – The reference mentions cold rolling with a 20% reduction, aligning with the 15%-80% range specified in US10190201B2.
- Copper is the Base Material – The alloy composition confirms copper as the balance, aligning with US10190201B2.
- Minor Additions of Elements – The reference discusses boron and other accessory ingredients, though exact weight percentages are unclear.
Feature | Disclosure Status |
The method involves casting a copper-nickel-tin alloy | Fully Disclosed |
The homogenized alloy is hot worked to obtain a reduction ratio of minimum 5:1 | Partially Disclosed |
The solution annealed alloy is cold worked until a reduction of area of 15% to 80% occurs | Fully Disclosed |
The alloy contains minor additions of boron, zirconium, iron, niobium, manganese, and/or magnesium, each not exceeding 0.3 wt% | Partially Disclosed |
The balance of the alloy composition is copper | Fully Disclosed |
Key Excerpt from the Reference:
“The copper alloy of the composition shown in the 1st table was dissolved, cast to the 30-mm-thick ingot, hot-rolled immediately after 1-hour heating maintenance at 850°C, and cold-rolled with a 20% reduction.”
Feature Comparison Table
Feature | US10190201B2 | JP2007531824A | JP2011503366A | BRPI0619666A2 | CN105714148B | JPH0413826A |
The method involves casting a copper-nickel-tin alloy | Fully Disclosed | Partially Disclosed | Not Disclosed | Not Disclosed | Fully Disclosed | Fully Disclosed |
The alloy is homogenized | Fully Disclosed | Fully Disclosed | Not Disclosed | Not Disclosed | Fully Disclosed | Not Disclosed |
The homogenized alloy is hot worked to obtain a reduction ratio of minimum 5:1 | Fully Disclosed | Not Disclosed | Not Disclosed | Not Disclosed | Fully Disclosed | Partially Disclosed |
The hot worked alloy is solution annealed at 1470°F to 1650°F | Fully Disclosed | Partially Disclosed | Partially Disclosed | Partially Disclosed | Fully Disclosed | Not Disclosed |
The solution annealed alloy is cold worked until a reduction of area of 15% to 80% occurs | Fully Disclosed | Partially Disclosed | Not Disclosed | Not Disclosed | Not Disclosed | Fully Disclosed |
The alloy is spinodally hardened after cold working | Fully Disclosed | Fully Disclosed | Not Disclosed | Not Disclosed | Fully Disclosed | Not Disclosed |
The alloy contains 5-20 wt% nickel | Fully Disclosed | Fully Disclosed | Not Disclosed | Not Disclosed | Fully Disclosed | Not Disclosed |
The alloy contains 5-10 wt% tin | Fully Disclosed | Fully Disclosed | Not Disclosed | Not Disclosed | Fully Disclosed | Not Disclosed |
The alloy contains minor additions of boron, zirconium, iron, niobium, manganese, and/or magnesium, each not exceeding 0.3 wt% | Fully Disclosed | Partially Disclosed | Partially Disclosed | Not Disclosed | Partially Disclosed | Partially Disclosed |
The balance of the alloy composition is copper | Fully Disclosed | Fully Disclosed | Not Disclosed | Not Disclosed | Fully Disclosed | Fully Disclosed |
The alloy has a 0.2% offset yield strength of at least 110 ksi | Fully Disclosed | Fully Disclosed | Not Disclosed | Partially Disclosed | Not Disclosed | Not Disclosed |
The alloy has an impact toughness of at least 12 foot-pounds when measured according to ASTM E23, V notch at room temperature | Fully Disclosed | Not Disclosed | Not Disclosed | Not Disclosed | Not Disclosed | Not Disclosed |
The alloy has an ultimate tensile strength of at least 120 ksi | Fully Disclosed | Fully Disclosed | Not Disclosed | Fully Disclosed | Partially Disclosed | Not Disclosed |
The alloy has a minimum elongation of 20% | Fully Disclosed | Not Disclosed | Not Disclosed | Not Disclosed | Not Disclosed | Not Disclosed |
How to Find Prior Art Using Global Patent Search
Locating relevant prior art is crucial for evaluating a patent’s validity. The Global Patent Search tool simplifies this process by offering precise feature mapping and in-depth search capabilities.
Here’s how you can efficiently find prior art references using the Global Patent Search tool:
#1. Conduct a search by Patent number or description – Input the patent number (e.g., US10190201B2) or relevant description to retrieve potential prior art.
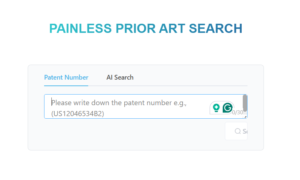
Source: GPS
#2. Utilize feature mapping – Compare the patent’s key elements against prior disclosures to identify similarities.
#3. Examine search results – Review a curated list of patents that could serve as prior art.
#4. Assess detailed reports – Analyze side-by-side feature mapping to determine whether an existing reference fully or partially aligns with the claimed invention.
With Global Patent Search, identifying relevant prior art is faster and more precise, making it an essential tool for patent litigation and invalidity analysis.
Win Your Patent Case with Data-Backed Prior Art Research
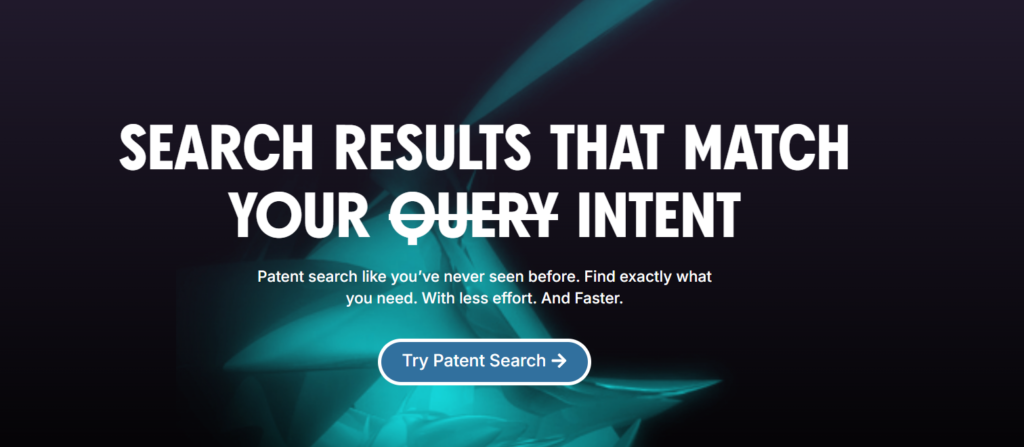
Patent disputes can be complex, but uncovering strong prior art doesn’t have to be. Global Patent Search empowers you with:
#1. Instant search results – Quickly retrieve relevant patents and applications.
#2. Accurate feature mapping – Identify key overlaps between the disputed patent and existing prior art.
#3. Comprehensive analysis – Strengthen your case with in-depth prior art comparisons.
Don’t leave your litigation strategy to chance. Equip yourself with data-driven insights and ensure you have the best prior art references at your fingertips.
Start your search with Global Patent Search today!
Disclaimer: The information provided in this article is for informational purposes only and should not be considered legal advice. The prior art references mentioned are preliminary results from the Global Patent Search (GPS) tool and do not guarantee legal significance. For a comprehensive prior art analysis, we recommend conducting a detailed search using Global patent search tool or consulting an established search vendor.